Our quality Socks manufacturing includes the following categories:
Hiking, Thermal, Diabetic, Compression, Casual, PC Melange, Athletic, Sports, Moisture Management, Anti Microbial, Yarn Dyed, Tecnical, Mesh and Arch Supports, Tecnical Logo designs.
Socks Stylings include:
- Crew
- Quarter
- Low Cut
- No Show
- Tube
- Thermals
- Diabetics
- Compressions etc.
Material consumptions include Cotton, Nylon, Polyester, Acrylic, Polyproplene, Lycra, Spandex etc.
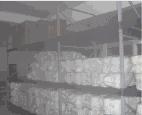
Yarn and Accessories Storage:
The 5000 square feet storage facility is equipped with state-of-the-art racking systems for both yarns and accessories. Before storage and issuance all materials are tested and inspected in the micro-lab by the quality department. To ensure optimum use of the storage, it is maintained with the most modern supply chain principles.
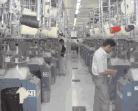
Knitting:
The knitting area covers a 10,000 square feet area with state-of-the-art Lonati 4 feed, 108-needle machinery. The area is equipped with a central suction system to increase the efficiency of the machinery and a humidification system to enhance the working environment for both the operators and the yarn. A workstation on the floor typically involves 1 operator working on 5-8 knitting machines, a quality supervisor to ensure optimum quality and a technical supervisor to maintain the machinery. Each pair of socks is inspected for quality by both the operator and the quality inspector. Lonati provides the latest design of software to program the particular design onto the machine. In addition, a special supervisor system is installed to monitor the production, efficiency, breakdowns and performances of each operator and workstation.
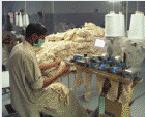
Linking: The linking section involves the seaming of the toe-end of socks. The state-of-the-art machinery has an automatic socks reversing attachment which helps improve the quality of the socks and minimize rejection levels.
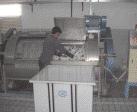
Bleaching /Dyeing: The 5000 square feet bleaching and dyeing facility is specially designed as a double rooftop in order to improve the working environment for the operators. The GREENMAC bleaching and dyeing machinery comes equipped with Y-shaped compartments to retain the same quality of bleaching and dyeing. Furthermore, it has frequency inverters which reduces the down time which in turn improves production, efficiency, and most importantly, quality. Other machinery for this process includes hydro extractors and dryers which are both specially designed by GREENMAC for socks.
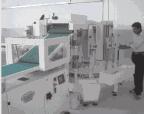
Boarding: The auto-boarding and pressing machine model 20P2 is the latest up to date boarding machine developed by Technopea. It has an average production capacity of 90 dozens per hour with an automatic conveyer belt system.
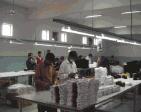
Finishing/Quality/Packing: The finishing department is where the final touches are made to the socks. Some of these final touches include tagging, printing (if required), quality inspection, sorting and packing.Once the socks have gone through this procedure, each pack is given a final check by the quality control department to ensure the order meets customer standards.
•In house state of the art Yarn Manufacturing Facility.
Unit 1: Blended Yarns (Ring Spinning) – 18200 Spindles
Unit 2: Cotton Yarns (Ring Spinning) -18000 Spindles
Unit 3: Re-Generated and Open End Yarn – 1600 Rotors (Open End and Auto Coro)
•Fiber Bleaching and dying to ensure consistent quality.
Vast Range of shades and colours at most competitive prices.
This facility gives us an opportunity to control the complete production process right from the grass root level to the finished product.
•Power Plant / Energy Systems
Our primary source is our in-house captive power plant of 4 Mega Watts to ensure constant supply of electricity with 2 backup energy supply systems.
Our boilers run primarily on waste heat recovery system based on our electricity power plant with 2 backups, Solid Fuel and Gas.
This setup ensures constant supply of electricity and gives us an edge over our competitors as we are one of the few manufacturers in the country with such a reliable energy / power systems to satisfy our customers with smooth operations and timely deliveries.